The main goal of the digitalization of manufacturing is to improve efficiency and increase owners’ income. According to McKinsey, successfully implemented digital solutions deliver irresistible returns. It is common to see 30-50% reductions in machine downtime, 10-30% increases in throughput, 15-30% improvements in labor productivity, and 85% more accurate forecasting.
This article discusses technologies that drive digital transformation in the manufacturing industry, case studies of digitalization, and how we at SoloWay Tech can help you digitally transform your business.
Key points
- What is digital transformation in the manufacturing industry?
- Technologies that drive digital transformation in the manufacturing industry
- What is necessary to create a digital twin for the factory?
- Case studies of digital transformation in manufacturing
- How can SoloWay Tech help you digitally transform your business?
- Conclusion
What is digital transformation in the manufacturing industry?
Digital transformation in manufacturing is the entire process from digitizing measurements and documents to creating new business processes that rely entirely on the digital twin data and the software that keeps it up to date. Digital transformation affects all factory areas and should be carried out gradually.
Nowadays, most of the data and documents are stored as files and digital data. The transfer of data previously provided on paper into digital form without changing the type and content of the data and documents is known as digitization. At this stage, there is no change in the existing business processes.
As technology is adopted, businesses receive more and more data in digital form. Eventually, it becomes possible to create a complete digital description of the manufacturing facility – a digital twin. The process of implementing digital technology to create this digital copy is called digitalization. The digital twin is created for all stages of the production life cycle, from design to operation and repair. Existing business processes are automated and accelerated with digital copy production data instead of documents and software.
As the digital copy becomes more accurate and complete, new efficient business processes are developed and implemented to replace the old ones. This is how digital transformation in manufacturing occurs.
Technologies that drive digital transformation in the manufacturing industry
Digital measurement and control systems have been implemented in the industry for decades, industrial Ethernet for over 20 years, and wireless networks for over 10 years. Computer technologies in the industry have evolved from isolated “islands” of control system networks and office computers to multilevel geographically distributed corporate networks with advanced access control and information security. Due to the development of cloud technologies and data centers, the problem of a limited amount of stored data and computing power is eliminated.
These factors make possible a large-scale technological transformation of manufacturing, often called Industry 4.0. Technologies that drive digital transformation in the manufacturing industry:
- Smart devices and Industrial Internet of Things (IIoT). They allow for obtaining comprehensive data about an object or equipment with its transmission to any other system, usually via wireless networks. The computing power of smart devices allows for implementing measurements and analytical calculations (edge computing).
- Digital twin. It is a full copy of an object at all stages of its life cycle, including drawings and 3D models in digital form, process models, data of current process parameters, and other vital parameters.
- Big Data. This technology for working with large volumes of heterogeneous data (time series, events, etc.) helps to analyze and obtain essential information for decision-making;
- Machine learning (ML) and artificial intelligence (AI). These technologies are necessary for training computer systems to find dependencies and apply them for decision-making. For example, ML can be used for fraud detection.
- Cloud technologies and services. They allow storing and processing of data, executing software services on a cloud infrastructure or in a corporate data center.
- Wireless and mobile communication technologies. The integration of wireless and mobile communication technologies is transforming the manufacturing industry by making it more agile, data-driven, and interconnected. It streamlines processes, reduces costs, enhances productivity, and opens up new opportunities for innovation and growth.
- Robotization. Advanced robotics systems, such as collaborative robots (cobots) and mobile robots, can be easily reprogrammed and redeployed to handle different tasks and production requirements. This flexibility allows manufacturers to respond quickly to changing market demands and adapt to new products or processes.
- Virtual (VR) and augmented reality (AR). These technologies help train employees, provide step-by-step instructions for complex tasks, and assist workers on the shop floor by overlaying digital information onto physical objects.
- Additive manufacturing and 3D printing. Additive manufacturing is an inherently more sustainable process compared to subtractive methods, such as CNC machining. It only uses the materials needed to create the object, minimizing waste and promoting eco-friendly manufacturing practices. 3D printing enables distributed manufacturing and on-demand production. Rather than relying on centralized production facilities and lengthy supply chains, manufacturers can decentralize production and manufacture closer to the point of use. This reduces transportation costs, lead times, and excess inventory.
In the first stages, the digitalization of the manufacturing industry encountered 1 key limiting factor. The main limitation was the amount of data that needed to be processed. This limitation applied to both the process of identifying correlations between data and the processing speed to ensure that management decisions are correct and timely. The main direction for solving this problem was artificial intelligence. AI allows manufacturers to work out many hypotheses quickly, using natural language processing for their construction.
What is necessary to create a digital twin for the factory?
A necessary but insufficient condition for the emergence of a digital factory twin is the formation of a data lake. This data lake should contain information from all levels of factory management. The key task of such a data lake is the synchronization of transactional data, representing the registration of events at the level understandable to a human (contract, application, order, product passport, equipment failure) and field data registered automatically by systems. Otherwise, this information cannot be used to obtain a full-fledged digital twin.
The main challenge of digitalization in manufacturing is the need to capture many events and facts that previously required manual data entry. And this is where modern digital technologies in manufacturing, such as machine vision, image recognition, and positioning, are beginning to play a decisive role. They enable events to be captured and translated into the data lake automatically.
An important consequence of the ability to enrich the data lake of a digital factory with more production data has been the possibility of using identical control algorithms for shop-floor and fabless manufacturing.
Case studies of digital transformation in manufacturing
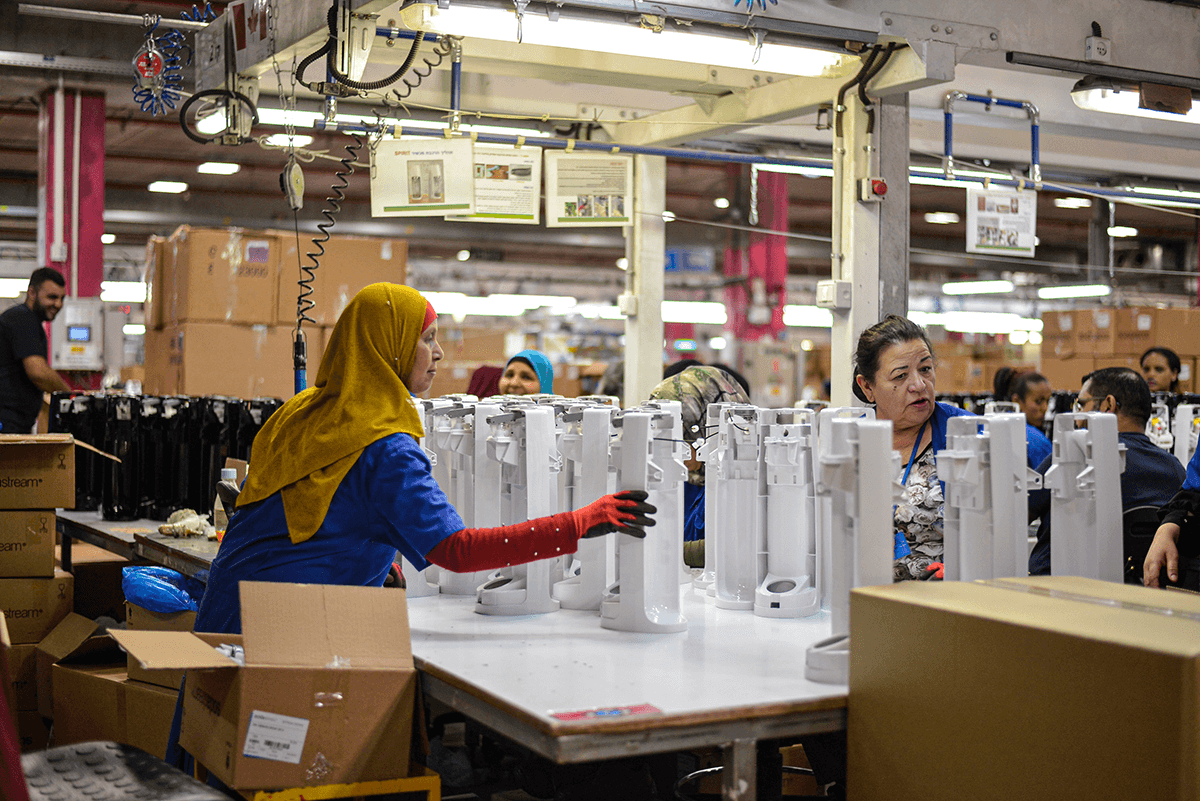
We have collected 5 top case studies on how manufacturers take advantage of digital transformation:
- General Electric (GE). GE embarked on a digital transformation journey to improve the efficiency and productivity of its manufacturing processes. They implemented a comprehensive Industrial Internet of Things (IIoT) platform called Predix. It connected their machines and equipment to collect real-time data. By leveraging advanced analytics and machine learning, GE gained insights into machine performance, predictive maintenance, and supply chain optimization. This allowed them to reduce downtime, optimize production schedules, and lower maintenance costs, significantly improving overall productivity.
- Siemens. This global manufacturing conglomerate has been actively integrating digital technologies into its operations. One of their successful digital transformation initiatives involved creating digital twins for their products and manufacturing processes. Using digital twins, Siemens improved product development, streamlined production, and enhanced product performance through data-driven decision-making.
- BMW. This automotive manufacturer adopted digital transformation to modernize their production lines and enhance their supply chain management. They integrated smart manufacturing technologies such as robotics, autonomous guided vehicles (AGVs), and IoT-enabled sensors across their factories. This increased production efficiency, reduced waste, and improved product quality. Additionally, BMW used data analytics to optimize its supply chain, allowing them to better forecast demand, manage inventory, and collaborate more effectively with suppliers.
- Haas Automation. This machine tool manufacturer embraced digital transformation to enhance customer experience and support. They developed a mobile application that allowed customers to remotely monitor their machines, access documentation, receive real-time notifications on machine status, and troubleshoot issues. By leveraging IoT and cloud-based solutions, Haas Automation improved customer satisfaction, reduced machine downtime, and provided more proactive support.
- Airbus. This leading aircraft manufacturer undertook digital transformation to improve the design and manufacturing of aircraft components. They adopted 3D printing technology (additive manufacturing) to produce lightweight and complex parts, reducing material waste and assembly time. Moreover, Airbus implemented virtual reality and augmented reality tools to optimize assembly processes and provide their workers with digital instructions and real-time guidance.
These case studies highlight how digital transformation can significantly impact the manufacturing industry by improving operational efficiency, product quality, supply chain management, and customer experiences. Manufacturers can stay competitive in an ever-evolving global market by leveraging cutting-edge technologies and data-driven approaches.
How can SoloWay Tech help you digitally transform your business?
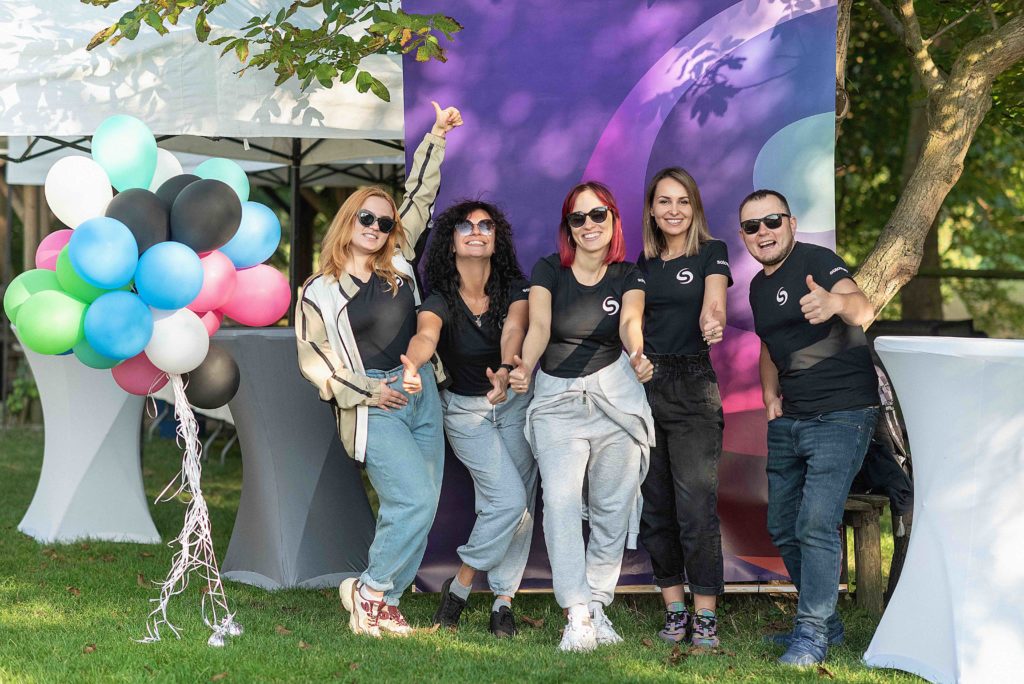
SoloWay Tech is a leading provider of digital transformation and consulting services for manufacturers looking to thrive in the digital age. Our extensive expertise and industry knowledge allow us to expertly guide your factory through the intricate digital transformation process, empowering you to uncover new opportunities and achieve sustainable growth. We can:
- Consult regarding the digital transformation of your business
- Develop a digital transformation strategy
- Design digital customer experience
- Optimize business processes
- Automate business processes
- Re-engineer legacy apps
- Develop innovative products and services
- Implement end-to-end ML and AI engines
- Engineer IoT
- Build Big Data infrastructure
- Consult regarding the best implementation of IT infrastructure in your business.
At SoloWay Tech, we understand the significance of this digital revolution and stand ready to be your partner in achieving a successful transformation. Our expertise in implementing smart devices, the Industrial Internet of Things (IIoT), digital twin technology, big data analytics, machine learning, and cloud services will empower your business to thrive in the digital age.
As demonstrated through case studies of leading manufacturers like General Electric, Siemens, BMW, Haas Automation, and Airbus, the benefits of digitalization are tangible and game-changing. By leveraging our services, you can improve production efficiency, optimize supply chain management, reduce downtime, and elevate customer experiences, thereby gaining a competitive edge in the global market.
Conclusion
The digital transformation of manufacturing presents unparalleled opportunities for businesses seeking to improve efficiency, reduce costs, and enhance overall performance. By embracing the array of cutting-edge technologies available, manufacturers can streamline their processes, gain valuable insights from data analytics, and revolutionize their operations.
The journey towards digital transformation may seem daunting, but with SoloWay Tech as your guide, it becomes a seamless and rewarding process. Together, let’s harness the power of digital technologies to drive innovation, growth, and prosperity in your manufacturing business. Embrace the digital age today and unlock a future of boundless possibilities.